Case study: Trinseo
Automation of one of the most modern plastics plants in Europe
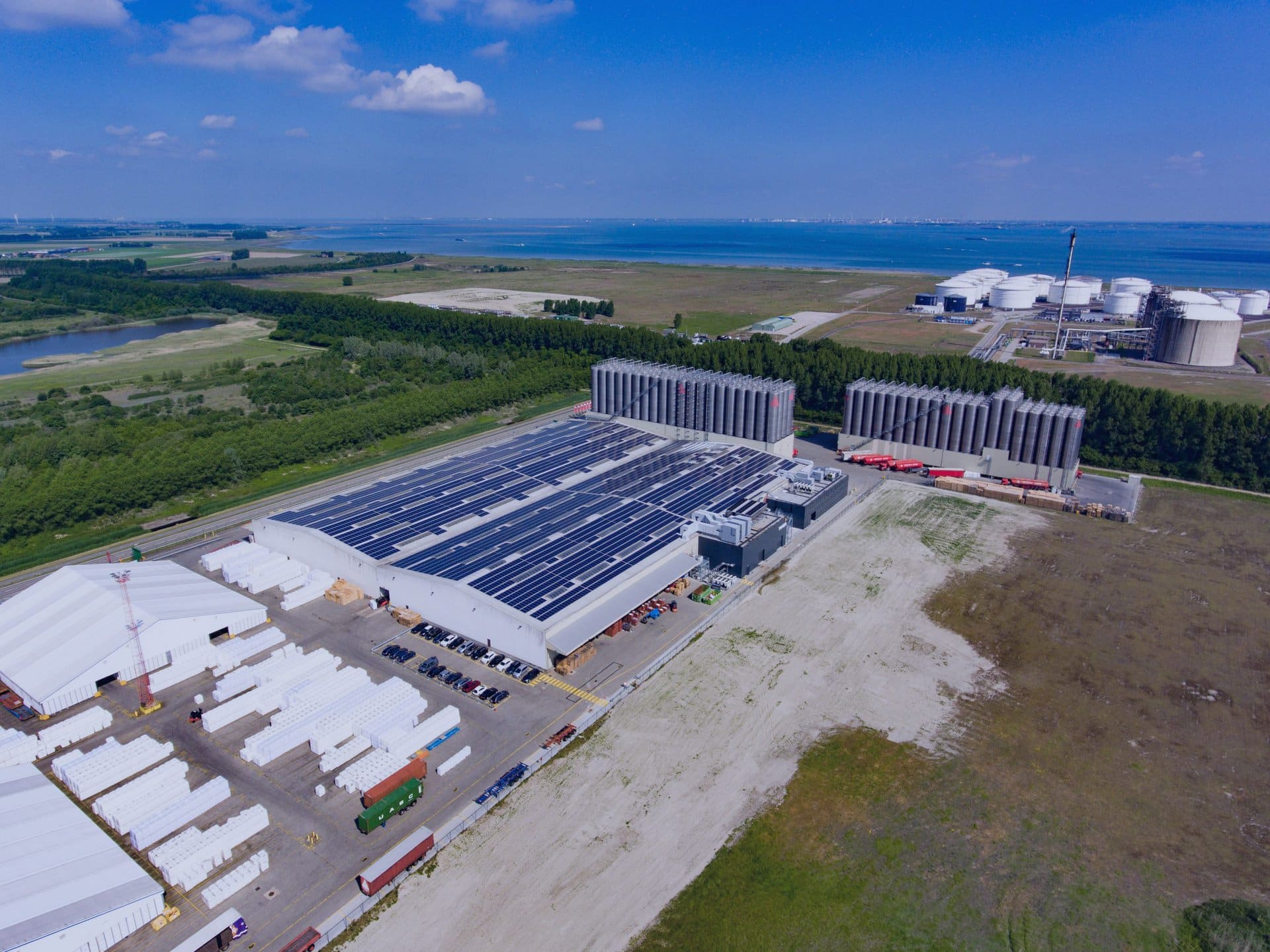
Results
Extensive use of state-of-the-art automation technology in the new plant enables significant resource efficiency and a smooth production flow.
Automation of material production and feeding enables significant improvements and reduces the need for manual intervention in discontinuous and continuous processes.
Digitizing production has significantly reduced data entry errors, eliminated multiple entries, and minimized manual data entry time.
About Trinseo
Trinseo Trinseo is a leading global supplier of high-quality plastics, latex binders and synthetic rubber. The company produces a wide range of products used in various industries such as automotive, electronics, construction, home appliances and packaging.
With state-of-the-art production facilities and advanced technologies, Trinseo is able to develop and deliver customized solutions for its customers. The company places great emphasis on sustainability and is committed to reducing the environmental impact of its production. Trinseo has offices around the world and a strong team of experts providing expert service and support to its customers.
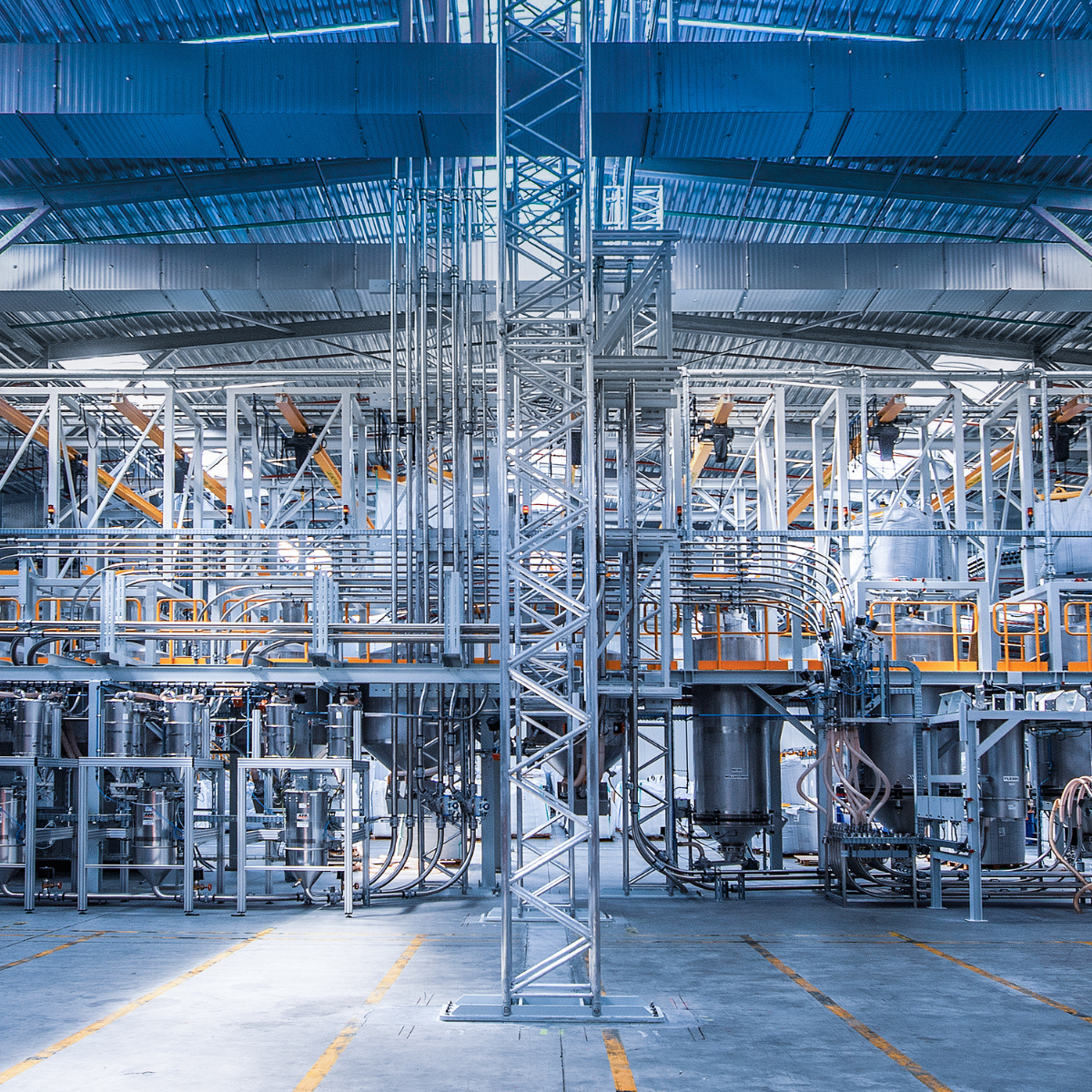
Why Trinseo came to BSG
As part of a greenfield project, a new plant was to be built to the latest standard.
Obsolete plant
The outdated plant no longer met modern automation and manufacturing technology requirements. The existing machines, control systems and production processes were outdated and not very efficient.
Complex production processes
The complex interaction of all plant components involved in the production process requires an end-to-end automation solution that brings together all plant components with as few interfaces as possible.
Manual data transfer as a source of error
The large number of end products requires specific plant configurations, each of which is divided into main and secondary orders. Here, data must be transferred manually, but this is often associated with a certain error potential and requires a considerable amount of time.
This is what BSG has made possible together with Trinseo
Thanks to the consistent use of state-of-the-art automation technology in all parts of production, the new plant is much more resource-efficient than the old one.
Initial situation
A batch process is used to produce a color-material mixture that is added to the main process. The production of this raw material component is largely self-sufficient.
End-to-end automation solution
Therefore, a solution had to be created that brings together all plant components with as few interfaces as possible. BSG has many years of experience and process competence in this area, both in PLC and IT project planning.
Large parts of BSG's engineering solutions were used in this project. These are divided into three areas. ONEoperate stands for the automation and operation of individual machines or entire production lines. Furthermore ONEview, which is used as a control system in the control room. The core of the entire automation is ONEexchange.
This software contains essential parts of an MES and connects all plant components with each other. In addition, it forms the interfaces to an ERP system, in this case SAP, and the laboratory information system LIMS.
Efficient order management
ONEexchange creates a bridge between competences of business planners and plant operators in production. An order consists of two parts in the Trinseo plant.
First, the main order for continuous production over the production lines. Furthermore, a secondary order - in this case a batch process for a color mixture, which is required for the main order. The division of the total order into main and side order takes place in the ONEexchange system.
The main order is assigned the production line and the corresponding production program within the production planning. The secondary order contains the details of the quantity required for the main order and also a driving program.
Automatic goods transport
Involved are almost 30 metering stations, an automated warehouse for color components, a manual metering station for very small quantities in the gram range, and finally a mixer that mixes the individual components in the mixing container. The transport of these mixing containers to the individual stations such as storage locations, dosing stations, mixers and production lines is carried out by several fully automated industrial trucks (AGV).
The management of the storage locations and their locations is organized in ONEexchange. The sequence of stations to be approached for a batch is also stored in this system. ONEexchange transmits the sequence to the AGVs, which approach these stations automatically.
Error-free batch process
Due to the automatic sequence of the batch process and the guided operation at the manual dosing station with plausibility check, errors in the batch process are nearly excluded. After completion of the batch, the mixing container is transported by an AGV to a specified storage location and is available for the main job on demand.
Flexibility for a wide range of requirements
However, the end products always consist of a main component and several secondary components, including the color mixture from the batch process. Feeding into the production lines is done from the raw material silos via several differential proportioning scales. In ONEexchange, the main orders are created. A production line and the corresponding driving program are assigned to a main order.
A driving program consists of all data necessary for production. Among other things, it contains dosing ratios of the required materials, temperatures of the tempering zones of the line, and speeds. These travel programs are stored in the ONEexchange database and can be easily assigned.
No more manual interventions necessary
ONEoperate includes complete automation of the production line, so that no data has to be transferred manually. After a short setup time, the main job is started by the operator of the line at the push of a button. From this point on, the entire rest of the process is automatic.
The line is started up via a step chain. The raw materials are fed fully automatically via corresponding, permanently installed conveyor paths and via the AGVs. Here, the raw materials are automatically brought to the appropriate removal points so that there is no interruption of the continuous production process.
Warehouse management and logistics
The mixes are parked on time by the AGVs in a rack system and automatically supplied just-in-time to the respective production line during production. During production, empty containers are likewise fully automatically replaced with full ones, allowing production to run continuously.
When production approaches the desired order quantity, the conveying of all raw materials is calculated and coordinated so that when the target quantity is reached, all containers and scales are almost empty. The advantage here is that no materials have to be disposed of at the end of the order.
Efficient cleaning and use of resources
The different start-up materials are also managed in ONEexchange. This material is stored in containers and reused by the AGVs as rework in the production processes. Either already in the currently running job or in the next suitable job.
As a secondary condition in this automatic process, there are materials that may no longer be used. These are collected and transported to a big bag loading point if the quantity is sufficient.
Material tracking and tracing
Thus, all materials of the total order can be tracked via the Track&Trace function. This includes both the materials from the main process and those from the batch process. The manufactured quantity of the end product is reported to the SAP system. The start-up material is also recorded in this way and can be returned to the production process depending on its quality.
Real-time monitoring and control
So-called information screens are installed at central points in the plant. On these, the most important data and statuses of the production plant, in particular of the production lines, are displayed on an overview screen.
Quality assurance and efficient reporting
Additional reports can be generated via ONEexchange. Besides warehouse or machine order report, also an OEE report is possible. The different plant statuses are transferred both automatically and manually from the ONEoperate system to ONEexchange.
In summary ...
The improvements for Trinseo are significant, as the necessary materials are produced, stored and fed to production fully automatically. The interaction between discontinuous and continuous processes requires hardly any personnel intervention.
The digitization of production has also significantly reduced the error rate of entered data. Once entered, data is made available digitally to all systems, eliminating multiple entries of the same data.
All of this results in a significantly more relaxed production process as well as optimized and more consistent workflows. In terms of Industry 4.0, Trinseo has taken a big step forward with the BSG systems and can look to the future with confidence.
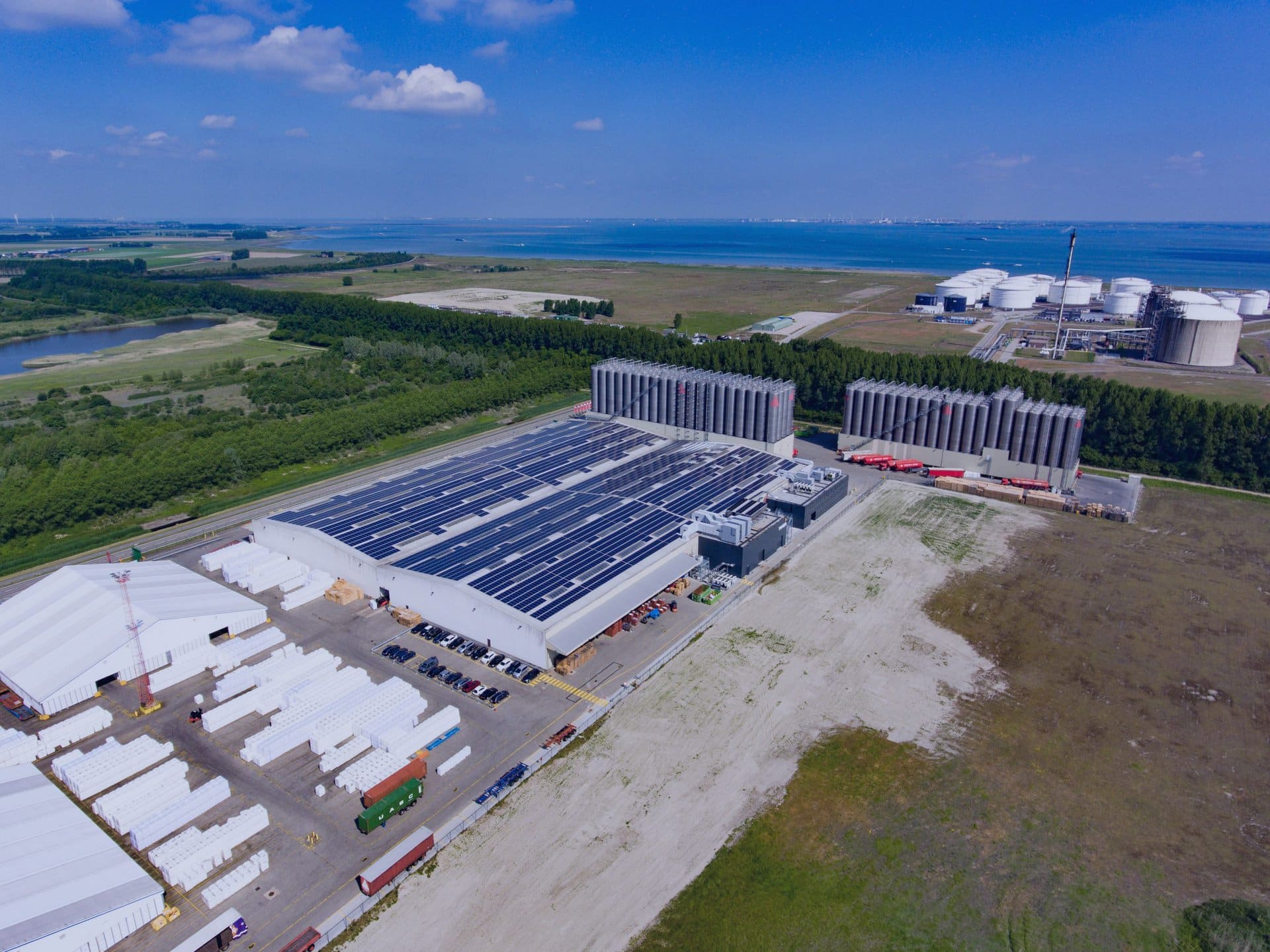