Case study: Jowat Corporation
From partial automation to retrofit to complete plant automation
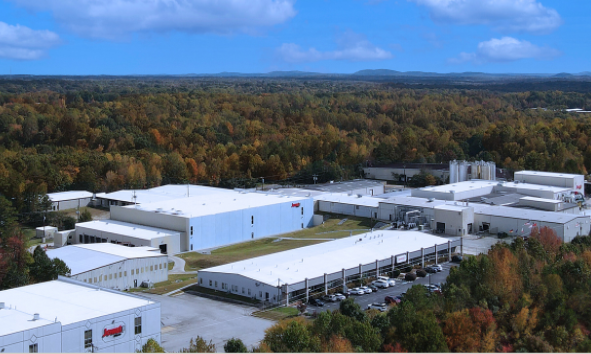
Results
Higher output can be achieved and scrap minimized.
The system can now be operated with just a few button presses and almost 100% tracking of the raw material is possible.
The system is significantly more robust and reliable thanks to the renewal of the cabling and the implementation of a reliable control system.
Improved availability of spare parts thanks to modern Siemens control system.
About the Jowat Corporation
Bonding is the most rationalizable joining technology and therefore a global growth market. As a medium-sized family business, Jowat SE is one of the world's leading manufacturers of adhesives. The products are used in particular in wood processing companies and furniture production, in the paper and packaging industry, the graphics industry, the textile and automotive sectors and the electrical industry.
The company was founded in Germany in 1919 and has expanded its activities worldwide. Its products are used successfully in over 80 countries on all continents. The full-range supplier produces 100,000 tons of adhesives annually with 1,250 employees. A global sales structure with 23 subsidiaries and partner companies ensures local customer support. With the tradition and experience of 100 years of company development, Jowat SE acts as a technology leader in many markets and fields of application.
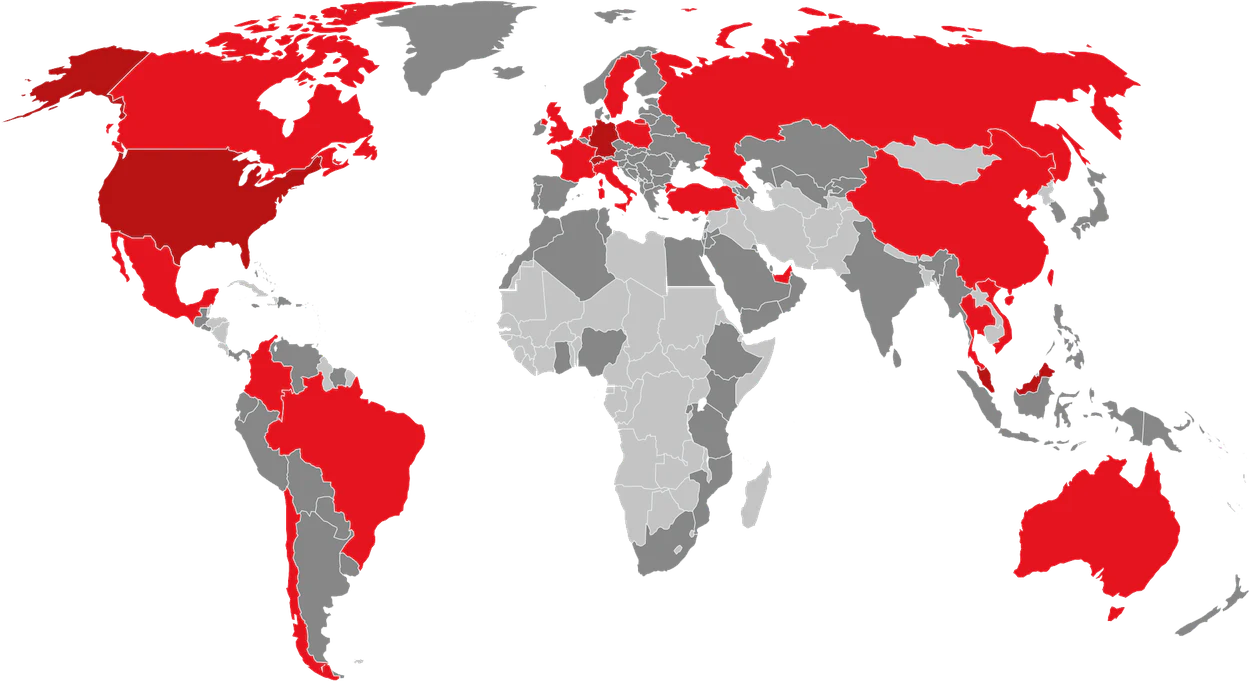
Why Jowat came to BSG
To ensure more efficient production, this extrusion line has undergone a comprehensive modernization. Jowat's main concerns were to further develop the system, increase capacity, raise the level of automation, carry out digitalization and restore the system's reliability.
Capacity too low
The old plant produced too little to meet the increasing demands.
Outdated operating concept
No tracking of material and more time-consuming analog operation.
Lack of reliability
Unwanted production downtimes due to outdated cabling and outdated control components.
Maintenance/repair difficulties
schwierigkeiten
The availability of replacement components was severely limited.
BSG made this possible together with Jowat
Concept development
Modernization of feeder systems and scales plus basis for overall automation
This step was commissioned remotely in October 2020 due to the COVID-19 pandemic. A special commissioning guide was created to support the customer on site during commissioning under the guidance of a BSG specialist.
Modernization of the extruder
The internal machine cabling was also renewed. The air conditioning system was also modernized to ensure optimum operating conditions. In addition, scanners for material and scales were integrated and an RFID login key system for user management was implemented on the control panel.
In addition, an underwater pelletizing system was added to the plant to further increase production capacity.
Commissioning was carried out on site by BSG commissioning engineers at the beginning of 2022.
Using the ONEexchange toolbox
ONEexchange links and manages the entire production process. A modular system is used to develop a solution tailored to the customer. Operators have access to the latest data and instructions at all times.
In addition, the efficiency of the system can be maximized by seamless recording of system data, recording of parameter changes and digital recording of process data.
Since the modernization, the system can be adjusted at the touch of a button with the consistency of data from management (ERP) to field level. Recipe/material changes are therefore completely paperless. Consumption data is available to management in real time and flows directly into planning.
In summary ...
The successful modernization of Jowat's extrusion line is an example of the continuous improvement and adaptation of production facilities to meet increasing demands. The use of modern technologies and the integration of intelligent solutions have significantly improved the efficiency, quality and reliability of the plant.
BSG remains committed to offering innovative solutions to provide its customers with an optimal production experience.
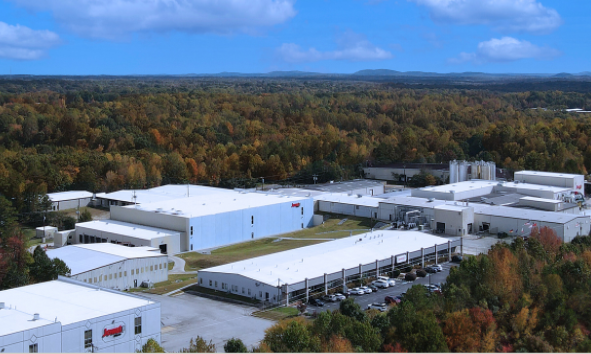