Case study: Polymer-Chemie GmbH
Retrofit of an extrusion plant
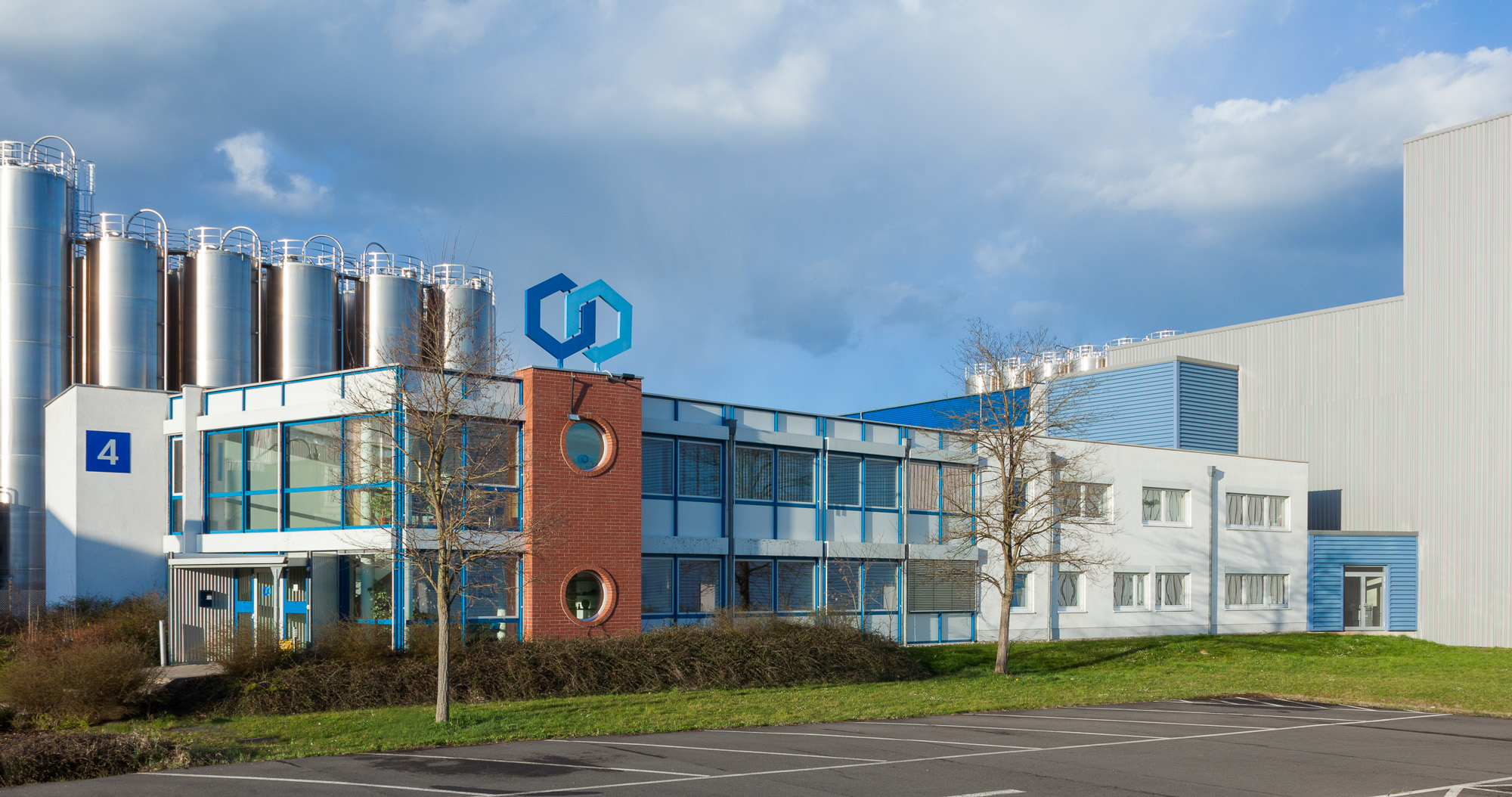
Results
The extrusion line now complies with safety standards.
The automation components are state-of-the-art, ensuring short procurement times for spare parts.
The line now has a modern user-friendly operating concept, which is also installed on the other plants of the company.
Here's why Polymer-Chemie chose BSG
The extrusion plant dated back to the 1980s, a time when there were no machinery directives prescribing safety standards for equipment. Due to the age of the plant, the control system was outdated. Additionally, many electrical components, including the entire switchgear, were no longer available as new items. Therefore, the plant could only be put back into operation after the defective components were repaired and reinstalled. This led to long downtimes and resulted in significant production losses.
Outdated plant without safety shutdown
The plant did not comply with the Machinery Directive and corresponding safety standards.
Outdated switchgear
Many electrical components were no longer available, leading to long downtimes in case of failure.
Outdated control system (analog operation)
The entire plant was monitored and operated solely through an analog control system using outdated control panels.
This was made possible by BSG in collaboration with Polymer-Chemie
Concept development
Modernization of switchgear systems
Modernization of the plant control system
RFID-Login
ONEdatagate implementation
In summary ...
These measures brought the plant up to current safety standards, enabling more efficient and secure operations.
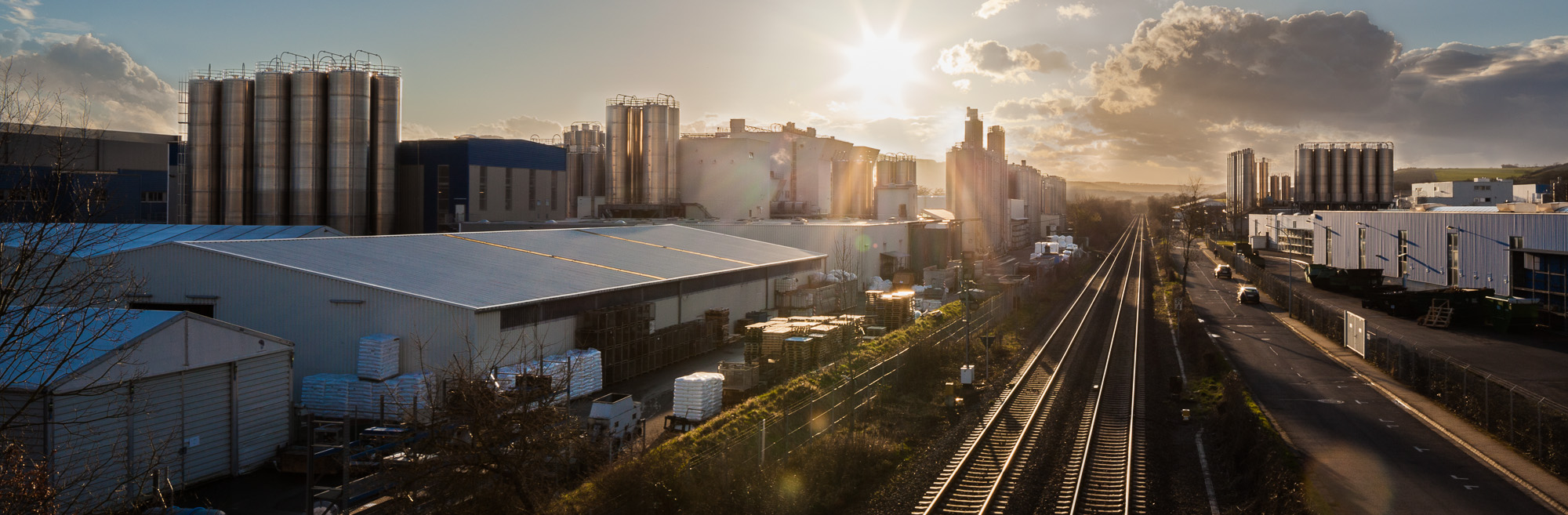