Case study
Retrofit of a compounding plant
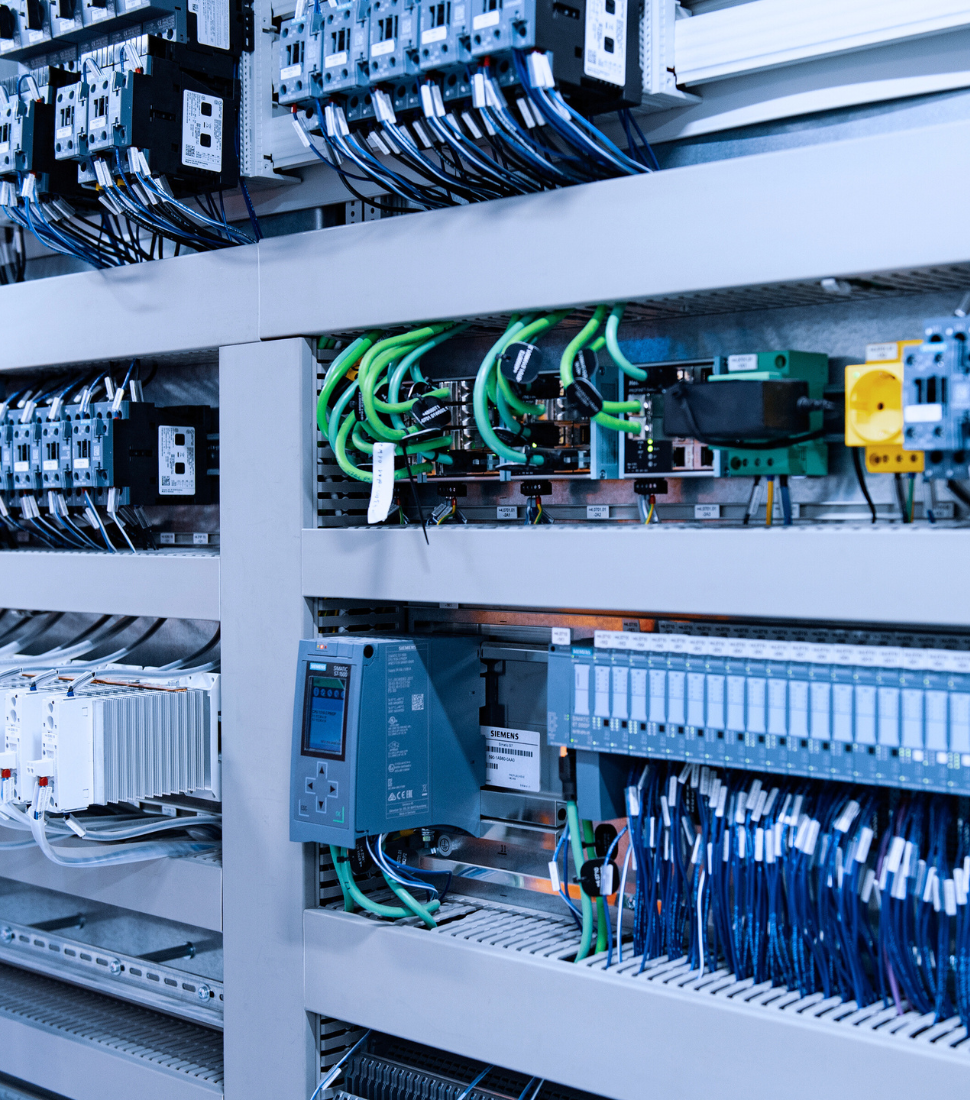
Results
The new compounding line is finally running without continuous downtime.
The software retrofit avoids unwanted production downtime and the desired added value has been achieved.
The company is now able to generate profits from the investment and realize the return on investment as the plant is running smoothly.
About the project
Our customer, who wishes to remain anonymous, has made a name for itself with innovative products and a strong customer focus in the field of masterbatch and compound for films and fibers.
We have been working together as partners for around 20 years and have automated several plants for our customer during this time.
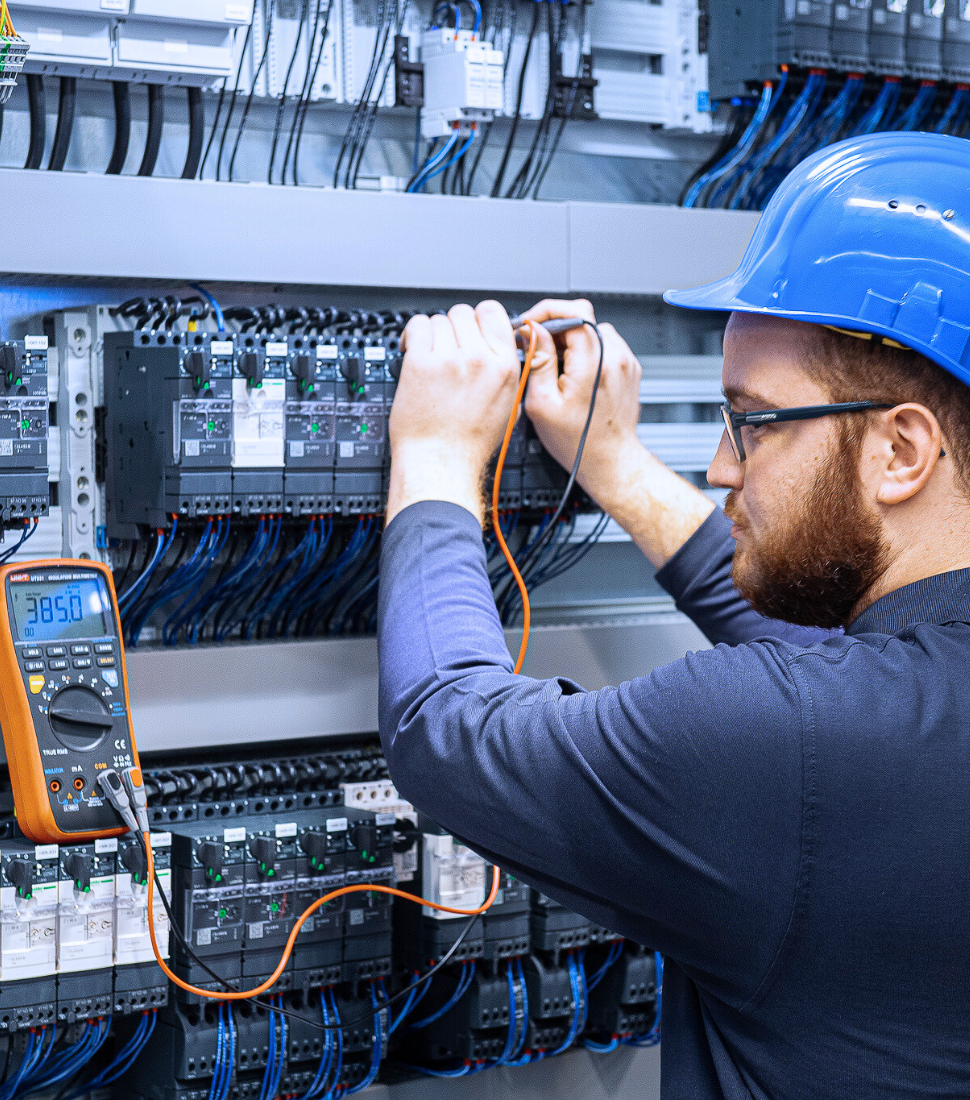
This is why our customer came to BSG
The customer invested in a new compounding plant in 2020. The manufacturer also supplied its own software control system for this, but there were frequent problems with it.
Constant production downtime
The low-quality control program meant that the plant had to be shut down several times. In addition, the electrotechnical interlocking did not comply with the German standard, for which the company did not receive acceptance.
High costs - no profits
The investment in this plant did not turn into the desired profit, but produced unwanted costs due to the constant loss of production, which in turn led to the constant interruption of value creation.
Inefficient processes
Another problem was that the installed control panel stopped working after a short time. Here, as a "quick solution", a PC had to be purchased as a provisional solution in order to be able to continue operating the system.
This is what BSG has made possible
Process of the retrofit
The existing CPU in the control cabinet had to be replaced with a larger CPU due to the memory capacity. Another important step was to retrofit remote maintenance using Siemens IoT to enable effective and fast troubleshooting. The rest of the plant remained unchanged, resulting in a cost-efficient solution.
ONEoperate as control software
In the trusting, long-term cooperation, BSG has successfully commissioned almost all other production lines with ONEoperate. Now, this line is also running with this innovative solution.
This gives the customer an overview of all plant components, parameters and process variables at all times. It provides intuitive access to all relevant information, allowing the compounding line to be controlled and optimized more efficiently. Another advantage is that the operating personnel can react to certain events directly at the central point.
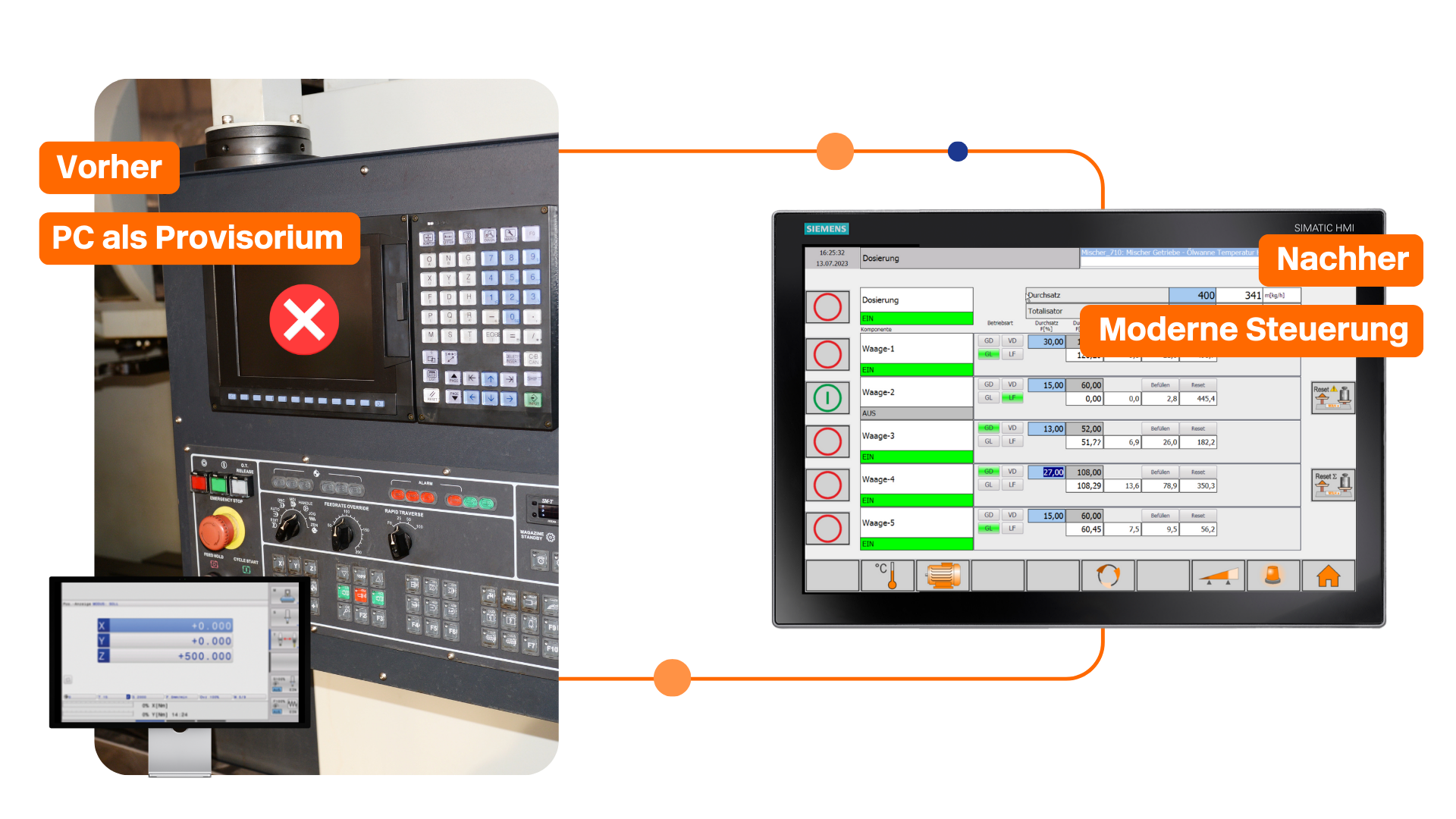