Case study: RP Compounds GmbH
Retrofit of a sophisticated extrusion plant
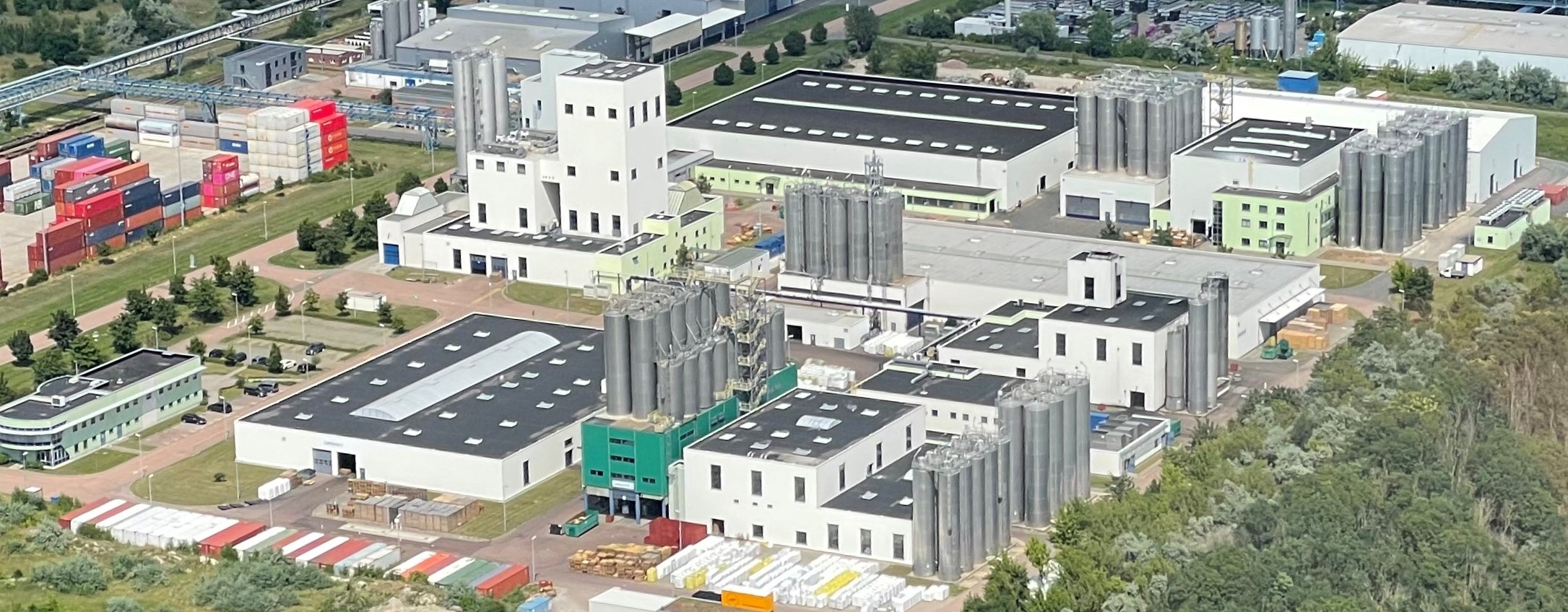
Results
By separating the conveyor technology for two production lines, it is now individually available for each line, enabling a parallel filling process from two silos.
Thanks to the modern S7 control system, the plant's safety now meets the latest standards, and spare parts availability has been restored.
The structure of the plant has now been overall decentralized, resulting in shorter cable routes everywhere, significantly facilitating fault diagnosis.
Through the digitization of the plant and the implementation of ONEexchange, weak points (process and data transmission via handwritten notes) and the resulting data loss have been nearly eliminated.
About RP Compounds GmbH
The RP Compounds GmbH (RPC), headquartered in Schkopau, Germany, is a renowned company specializing in the manufacturing and distribution of high-quality plastic compounds, providing tailored solutions to a variety of industries. As a member of the Ravago network, RPC is part of a leading service provider in the plastics and rubber industry.
With its extensive experience in the plastics industry, RPC has earned an excellent reputation as a reliable partner, focusing on quality, sustainability, and social responsibility.
The company was founded in 1997 and today, with over 140 employees, is a significant employer in the region.
RPC supplies customers worldwide and is characterized by high flexibility and fast delivery times. With its wide product portfolio and international orientation, RPC is well positioned to meet the market's demands and continue to grow successfully.
In doing so, RPC relies on state-of-the-art technologies and production processes to ensure high product quality.
Here's why RPC chose BSG
Due to various challenges in the plant for manufacturing high-purity plastics, RP Compounds decided to collaborate with BSG
Outdated plant concept
The plant cannot be effectively utilized due to integrated conveyor technology on two production lines.
Outdated technology
Due to the outdated control components, the plant's safety does not meet modern standards, and spare parts are scarcely available.
Downtime due to elaborate troubleshooting
The remaining centralized structure with long cable routes led to elaborate troubleshooting with prolonged downtime.
Time and data loss due to analog data management
Analog recipe management and product tracking are time-consuming and carry a high risk of data loss.
This was made possible by BSG in collaboration with RPC
Modernization of the plant
Additionally, remote maintenance was retrofitted to enable quick support. New control panels with updated visualization for simplified operation of the plant were also installed.
Conversion of the plant concept
Additionally, the conveyor technology was separated from two production lines, making it now individually available for each line. Moreover, a new plant expansion was directly implemented into the new control system.
Integration of ONEexchange
Operators have access to the latest data and instructions at all times. Additionally, the efficiency of the plant can be maximized through seamless capture of plant data, recording of parameter changes, and digital recording of process data.
The integration of ONEexchange now enables RP Compounds to have digital raw material and product traceability, providing automatic reports for improved quality management.
In summary ...
Overall, the collaboration with BSG has helped the customer modernize its plant, optimize production processes, thereby increasing plant availability and maintaining product quality.
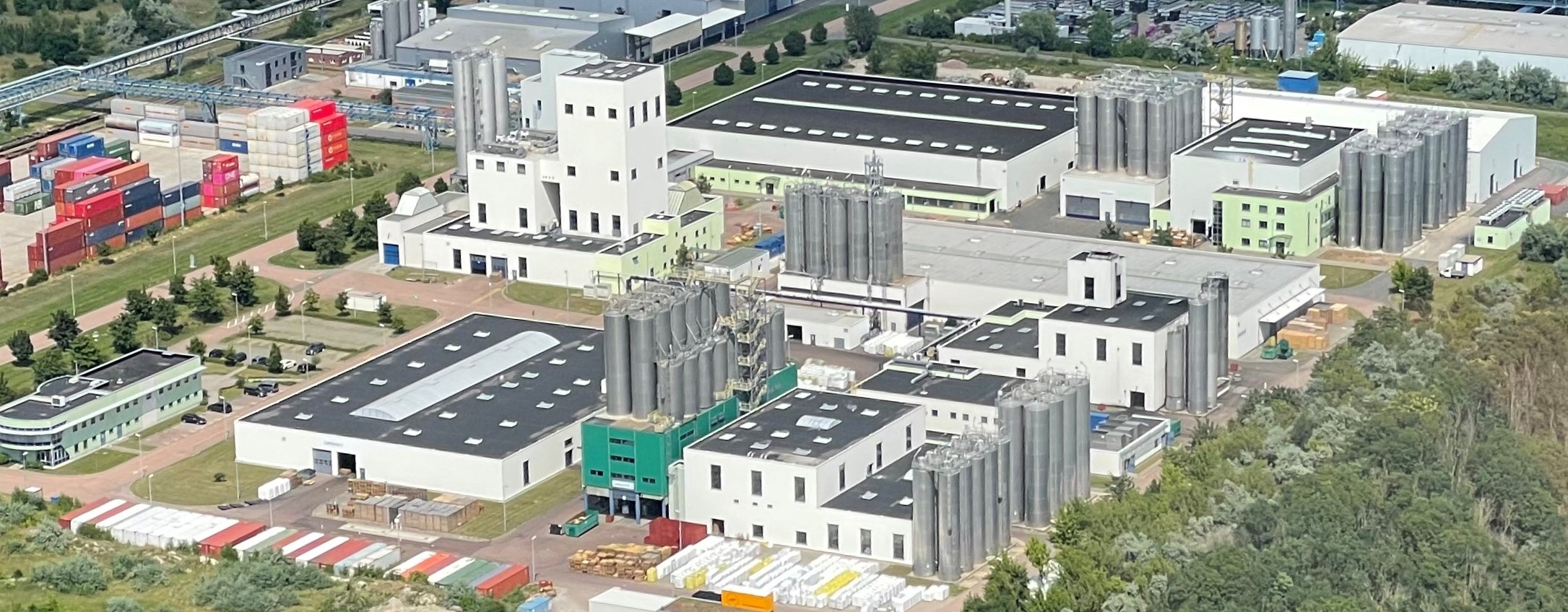